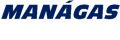
Complete Guide to Gas Mixers and its various applications
Why is MIG welding (GMAW) better than TIG welding (GTAW)?
When comparing MIG welding (GMAW) process and TIG welding process (GTAW), we noticed that there are several variations of electric arc welding processes, as well as a multitude of variations in welded parts, and determining the most suitable welding process is vital for a project to be successful.
Although the electric arc is used in both MIG and TIG welding, the processes are quite different.
TABLE OF CONTENTS:
Both, MIG (GMAW) and TIG (GTAW) welding processes uses an electric arc to create the weld. The difference between the two is the way the bow is used. MIG (Inert Metal Gas) welding uses a supply wire that constantly moves through the gun to create the spark, melt the metal and form the weld’s melting pool.
In the case of TIG welding (Tungsten Inert Gas), it uses a non-consumable solid electrode to weld two metals.
1. MIG Welding - Variety of jobs
Although TIG welding can be used on more types of metals, its effectiveness is limited in thicker jobs. On the other hand, MIG welding can be used to weld various materials, for example aluminum, stainless steel and carbon steel and in all thicknesses, from number 26 plates (0.5 mm) to heavy duty thick plates.
MIG welding has this great advantage over TIG because the wire feed acts not only as an electrode, but also as a filler. As a result, thicker parts can be melted without the need to heat them up completely. And because it uses fill instead of fusion, MIG welding can be used to weld two different materials.
2. MIG Welding (GMAW) - Productivity and Speed
Another reason to choose MIG welding instead of TIG welding is speed. A MIG gun is designed to work continuously for long periods of time, making it more efficient and productive than a TIG gun or torch. For large industrial operations that require high productivity, MIG welding is the ideal option.
Additionally, MIG welding works very well in automated welding processes.
On the other hand, TIG welding is a much slower process, capable of welding parts with small details.
3. MIG Welding (GMAW) - Lower Welding Cost
As with any production or manufacturing job, welding time equals money. Therefore, taking into account that the MIG welding process is much faster than TIG welding, it is possible to conclude that MIG welding will also be more competitive, more economical. Parts welded via the MIG welding process are also more productive and less costly when compared to the same steps performed with TIG welding.
4. MIG Welding (GMAW) - Reduced Learning Curve
Another very important point to consider, MIG welding is easier to learn and can be improved after just a few weeks of training. Due to the ease of the process, the MIG weld is called “hot glue gun” welding as it is enough to press the trigger to start or stop the weld. MIG welders can hold and operate the gun with just one hand, making it an ideal option for novice welders.
On the other hand, TIG welding requires a more specialized technique, where in some cases it requires the use of hands and feet for separate activities (starting or ending the arc, feeding the melt pool, etc).
QUESTIONS related to “Why is MIG welding (GMAW) better than TIG welding (GTAW)?”
Any questions and comments related to “Why Is MIG welding (GMAW) better than TIG welding (GTAW)? Please feel free contact us at any time. In addition, please take this opportunity to explore our product line of high performance gas mixers for MIG welding (GMAW welding).
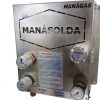
Gas mixer designed and manufactured for the welding process, which allows mixing between 02 gases, with flow rate and outlet pressure control. From 0 to 100% content adjustable gas mixing output.
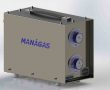
Compact gas mixer designed and manufactured for the welding process, which allows mixing between 02 gases, with outlet flow rate control. From 0 to 100% content adjustable gas mixing output. Requires cylinder/first stage pressure regulators for both input gases.